Products
Our Solutions
Isochemicals provides a comprehensive range of Polymer, Molecular, and Halogen-Free flame-retardant masterbatches for use in the production of XPS (extruded polystyrene) and EPS (expanded polystyrene).
The masterbatch production technology offers many technological and environmental benefits compared to other products (such as powders) used in the manufacturing process. It ensures maximum performance, enhances flame-retardant effects, and improves the physical properties of the finished products.
All flame retardants for XPS and EPS produced by Isochemicals are high-quality products that deliver consistent and superior performance. They can also be customised to meet the specific needs of customers, ensuring tailored performance for each unique production process.
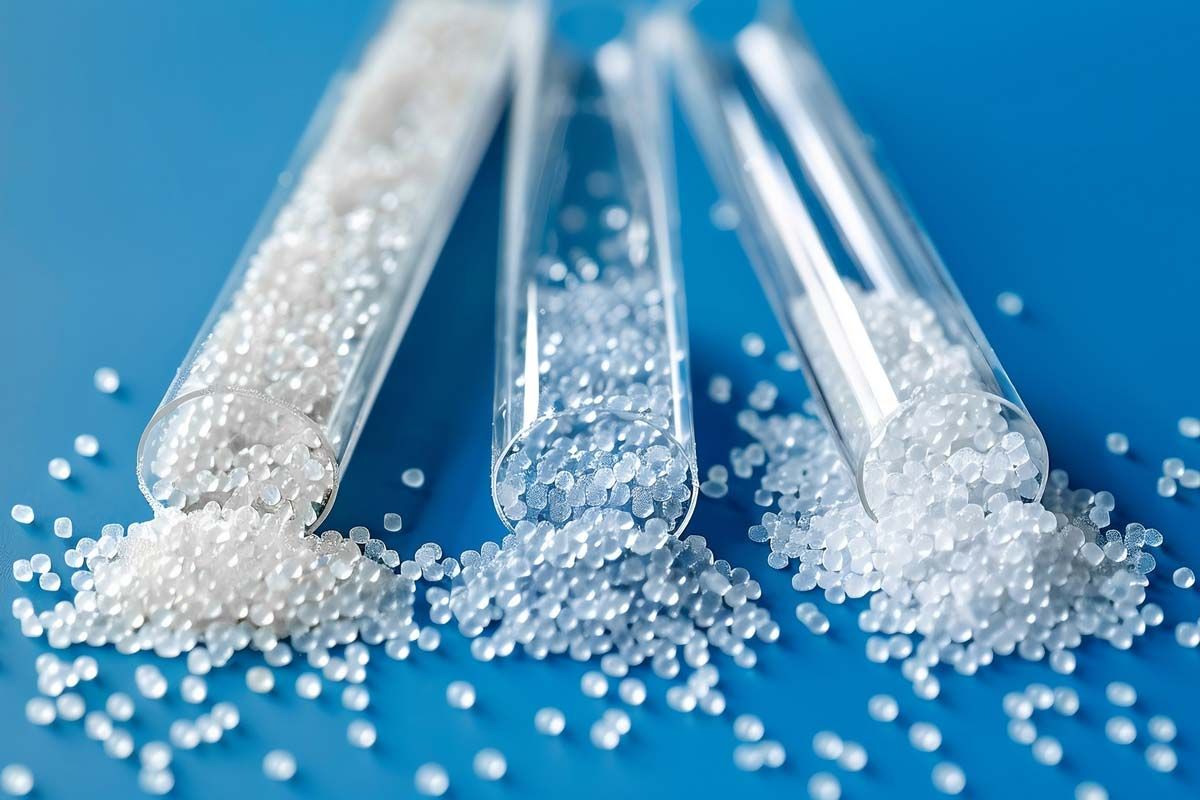
Why Choose Masterbatch?
Using masterbatch in the production processes of plastic components offers numerous advantages. Here are the key benefits:
-
Enhanced Product Properties: Masterbatch improves the mechanical and thermal properties of additivated XPS and EPS products, ensuring high resistance to elevated processing temperatures and uniform dispersion during production.
-
Cleaner and Easier Material Management and Handling: Opting for masterbatch instead of powders keeps the workplace and production cleaner, reducing the effort and cost associated with cleaning equipment and the work environment.
-
Better Distribution of the Product in the Final Application: Flame retardants and other additives are uniformly dispersed throughout the polymer matrix, ensuring reliable and consistent performance of the final product. Homogeneous distribution also maximises the effectiveness of the additives, guaranteeing consistent product quality.
-
Safer: Using our flame-retardant masterbatches eliminates the exposure risks associated with some powders and liquids. Additionally, the absence of powders improves production safety, thus reducing the environmental impact during production.
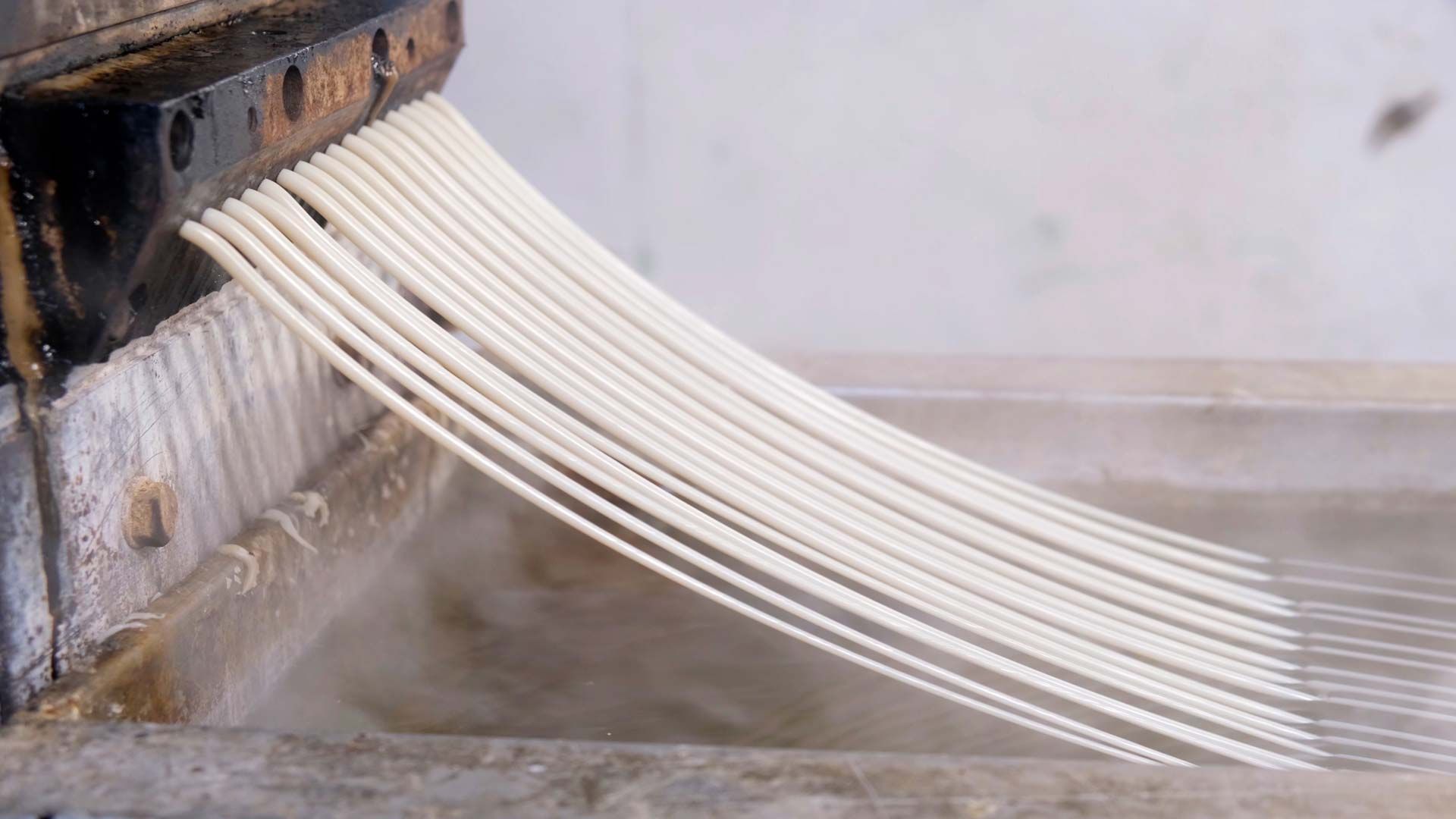
Our commitment to a green, sustainable approach, as well as strict compliance with current regulations, drives us to offer a complete range of polymeric masterbatches made with raw materials sourced from authorised major suppliers.
At the same time, we provide a full portfolio of solutions, including molecular masterbatches. We are also working on halogen-free solutions, which will soon be introduced to the market.
Our goal is to offer our customers a broad range of solutions for their production needs, supporting them with customised products, backed by expert technical service and an advanced in-house R&D laboratory operated by highly qualified technicians and researchers.
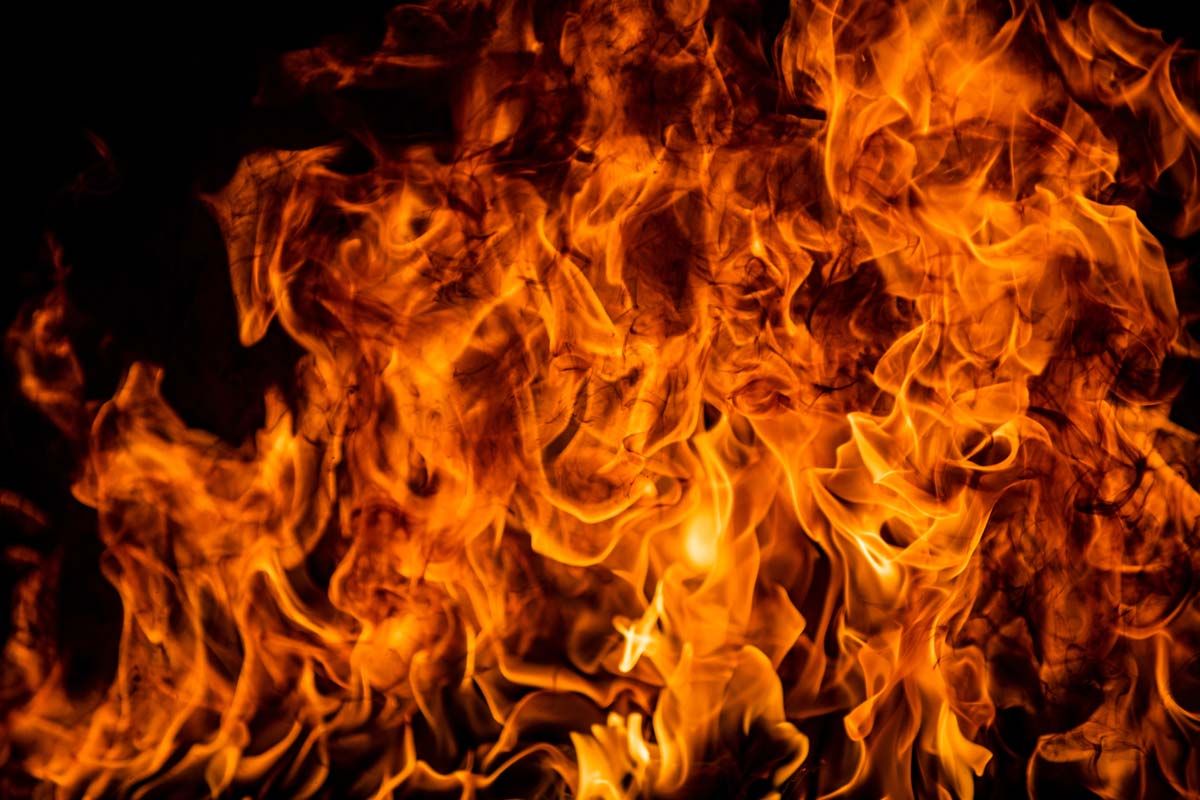
Our Product Range
Our flame retardants for polymers are divided into three categories:
Polymeric
These flame retardants are produced using raw materials from the three authorised global manufacturers. The range is extensive, with each product designed to meet specific production needs.
Over the years, our formulations have evolved, and in collaboration with our customers, we have developed increasingly customised products to address diverse production and performance requirements (e.g., different fire resistance classifications).
Among brominated flame retardants, polymeric variants stand out for their reduced environmental impact, as the bromine is embedded within the polymer structure, which is essential for better sustainability.
Our suppliers are:
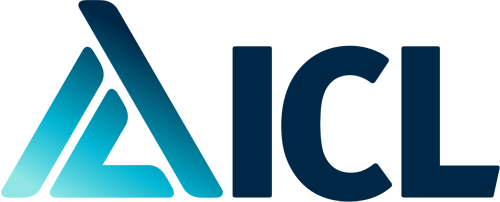
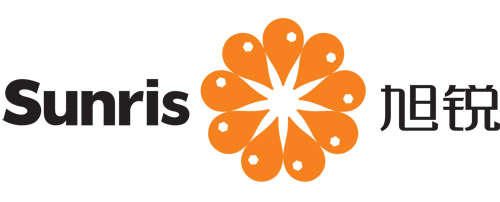

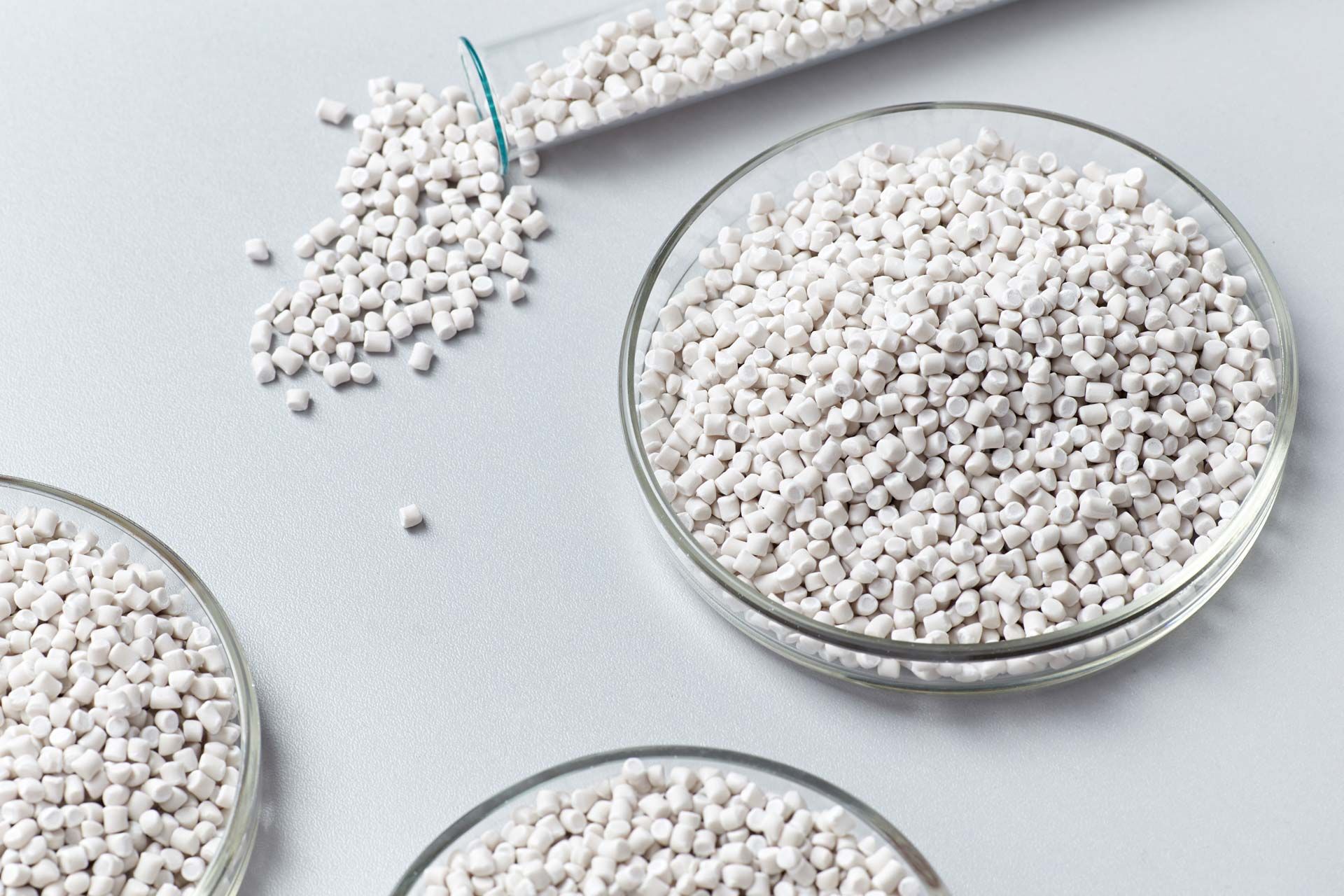
Molecular
These flame retardants are made from monomeric raw materials. Available in various formulations and concentrations of active ingredients, these products offer the best value for money.
Halogen-Free
These are the future of flame retardant additives, and we are already working on them, with plans to launch them on the market soon.
Our Products
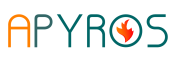
This is our registered trademark that identifies our long-standing flame retardants for EPS and XPS production applications.
GREENCELL
It represents our nucleating masterbatches, available in various particle sizes according to customer requirements.
GREENFAST
This is our processing aid masterbatch, designed to improve the homogeneity and surface quality of XPS sheets, reducing friction and preventing overheating within the extruder.
Some History
Before 2015, the flame-retardant additives used in the production of masterbatches for XPS and EPS manufacturing were all based on HBCD. This raw material was banned in Europe in August 2015, and Isochemicals immediately responded by introducing new Bromine-based polymeric masterbatches without HBCD content, known as HBCD Free.
These new products, developed in-house by our Research and Development laboratory, have evolved and improved over the years to better meet the specific needs of our customers while fully complying with European regulations. This versatility has allowed us to proudly lead the plastic additives market, thanks to the variety and reliability of our solutions, which cater to a wide range of production performance requirements.